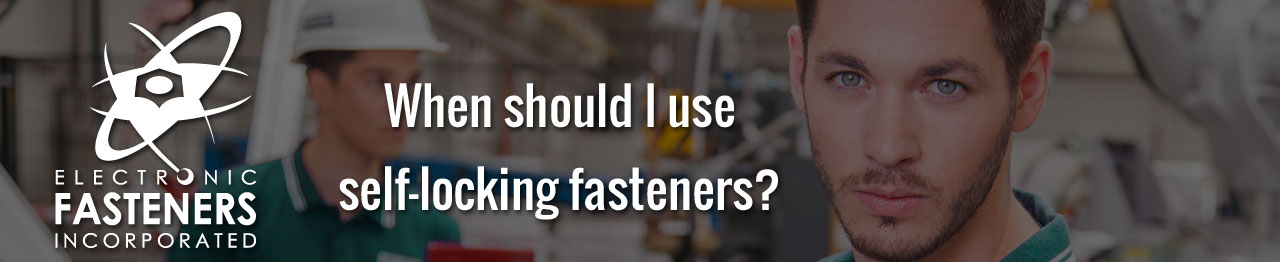
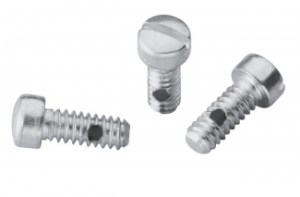
Self-locking fasteners have a number of advantages over other kinds of fasteners, including greater reliability and holding power. They are used primarily in situations where good pullout and torque loads are required, especially in thin sheet metal that can’t be securely fastened by other means. In many cases, self-locking fasteners – because of their locking power, low profile, and compact design – can enable the use of even thinner sheet metal for a lighter and smaller assembly form factor.
Self-locking fasteners are the ideal fastening solution for applications in which the attaching hardware can’t be easily reached after a cabinet, chassis, or other component is assembled. Self-locking fasteners can be installed during fabrication to simplify and speed up assembly operations and component mounting, especially for equipment installations and replacements performed in the field.
Manufacturers should consider self-locking fasteners for products in which simplified assembly and fewer parts can reduce production costs and speed up time-to-market in highly competitive marketplaces. Self-locking fasteners not only reduce labor time, inventory and overall product weight, they also provide greater product design freedom enabling the use of thinner metals. All of this makes self-locking fasteners especially attractive for medical, computer, communications, automotive and aerospace products.
Self-locking fasteners should only be used in products utilizing a metal that is softer than the fastener. For a self-locking fastener to work correctly it must cold-flow the softer sheet material to form a secure bond. If the self-locking fastener is softer than the sheet metal, it will simply deform and not work properly. Products incorporating stainless steel sheet metal require self-locking fasteners designed specifically for stainless.