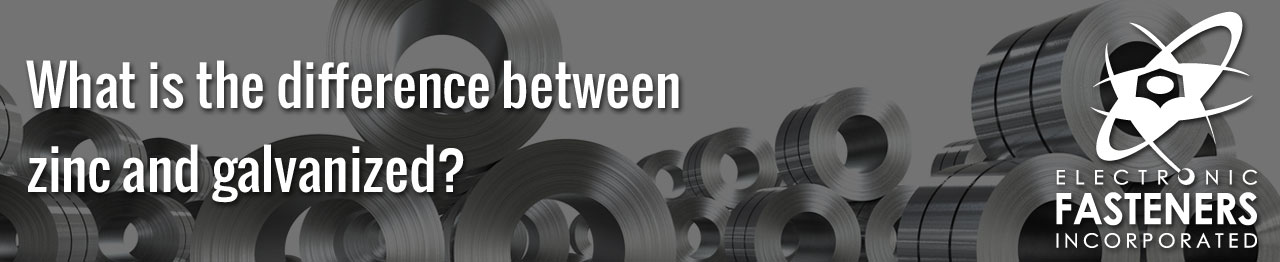
All true galvanizing is hot dip galvanizing. Parts to be galvanized are submerged in molten, liquid zinc; hence the name “hot dip”. After 20 years outdoors a galvanized product will not show signs of rust. The galvanized product will develop a white protective coating (zinc oxide) that adds to its protective properties.
Zinc plating has found wide acceptance as a surface finish for consumer, industrial, and commercial products. The relatively low cost, protective nature and attractive appearance of zinc plating make it a popular coating for nuts, bolts, washers, metal stampings, automotive components and fabricated parts for industrial applications.
Commercial Zinc is the name or label given to a zinc finish specification that is commonly used in finishing metal parts. When specifying “Commercial Zinc”, you get a basic range of zinc finish protection. The normal composition has a thickness of .0002” of electroplated zinc. Additionally, some commercial zinc formulations add a chromate top covering to protect the zinc finish.
Post-Plate Chromate treatments are used primarily to improve corrosion resistance, improve paint or adhesive bonding properties, and provide a decorative or colored finish. After the zinc plating, and chromate has been applied, a post-plate “sealer” can be applied that will significantly enhance the corrosion protection. The Sealer chemically bonds with the chromate film to seal and harden chromate films as well as increase their adhesion to zinc surfaces.