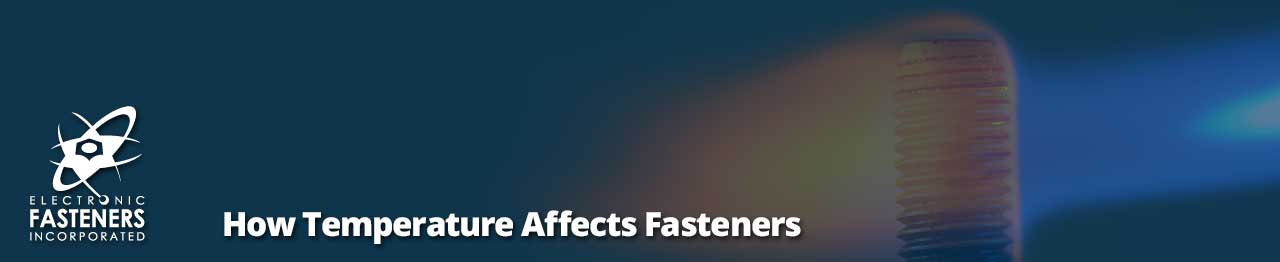
When designing construction projects or equipment for any application involving very low or high temperatures, it’s especially important to consider the effects these temperatures will have on fasteners and the metals used to manufacture them. There are many fastening applications utilizing nuts, bolts, screws, rivets, clamps, hinges, anchors, and other hardware that may be exposed to extreme temperatures, so choosing the right ones can be critical.
In colder locations, for example, sub-zero temperatures can affect the strength as well as the ductility of a fastener, which may cause it to become brittle. Low carbon steel that has Grade 2 strength, for example, shouldn’t be used if it is going to be exposed to extreme cold. As temperature decreases, many materials shift from ductile to brittle behavior at the ductile-to-brittle-transition-temperature (DBTT). Obviously, shattering is more likely to have negative consequences, compared with deforming, and at very low-temperature steels generally tend to be more sensitive to impacts, with a risk of breaking in case of a sudden shock or bending.
Interestingly, lower temperature frequently results in an increase of mechanical tensile strength of metal and less elongation at break. To keep the mechanical strength high and achieve a less brittle material, austenitic stainless steels with a high content of nickel and nitrogen are generally preferred.
In extremely hot and humid environments, fasteners that contain iron and plastic fasteners should be avoided and instead, steel and medium carbon fasteners should be used for applications. An added benefit of choosing stainless steel fasteners is that stainless steel is corrosion resistant. At extremely high temperatures, there are some temporary phenomena that occur, while others are permanent. Reversible ones, which regress if the temperature returns to what is considered normal, include a temporary loss of mechanical tensile strength and changes in ductility.
Characteristics known as “creep” and “relaxation” can also be triggered by high temperatures. Creep is when a material deforms slowly and permanently due to constant mechanical stress, even though it is below the material’s yield strength. Relaxation is when the material, even though it is initially loaded below its yield strength, releases stress when exposed to a fixed strain by transforming a portion of this elastic deformation into plastic deformation.
Creep or relaxation in metals both occur more readily if subjected to higher temperatures, even before the loads or deformations exceed the yield strength of the material – how much creep or relaxation depends on the amount of stress, the temperature, and exposure time. These phenomena can be activated from about 200°C for steels and as low as just over 100°C for some light alloys and stainless steel. To address these kinds of challenging conditions, designers may choose to use creep-resistant alloys that are nickel-based or cobalt-based. It’s important to note that creep and relaxation permanently modify the parts in terms of deformation or stress relief.
Temperatures affect different fasteners in different ways. With some basic knowledge, you can make good choices when it comes to choosing fasteners to hold together a building or a piece of machinery. To learn more, contact the fastener experts here at Electronic Fasteners.