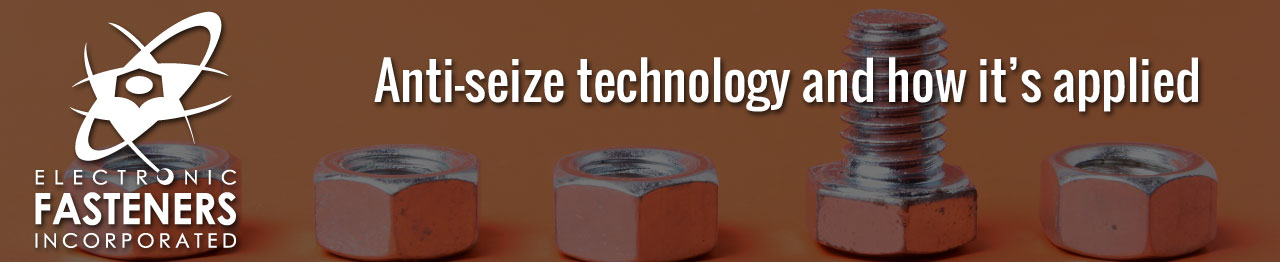
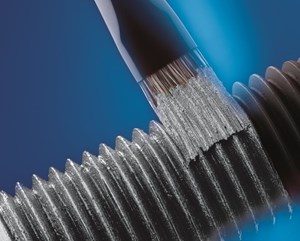
Anti-seize technology really has just two major elements: some sort of lubricant combined with one of any number of solids, especially metals, that feature a low coefficient of friction. The anti-seize compound is brushed onto bolts or other fastener components to prevent the corrosion that can hinder the two parts from sliding past each other, causing them to “seize” and become immobile. However, once anti-seize technology is applied, the lubricant used evaporates over an often short period of time, leaving behind the solid elements which help reduce friction and adhesion, enabling the fastened components to disengage and reengage easily. When anti-seize compounds are not used on fasteners in many harsh environments, corrosion and seizing can be so great that fastener heads have to be cut off and bolts drilled out, destroying the fastener and often rendering useless the components fastened together.
To ensure that anti-seize technology is used correctly, choosing the right anti-seize compound and applying it properly is vital. Initially, most anti-seize compounds contained copper and graphite or copper, aluminum, and graphite, which worked well for most applications in standard situations. These anti-seize compounds were ideal for high temperature applications since aluminum can withstand temperatures up to 1000 °F, copper to 1800 °F, and graphite over 2000°F. However, since copper and aluminum are reactive metals, they were not suitable for some applications exposed to substances like acetylene and ammonia.
For extremely high temperature applications or those in which a non-reactive compound was needed, special anti-seize compounds such as nickel or molybdenum disulfide (moly) were developed. Nickel is chemically inert and can withstand temperatures to 2600 °F. Moly is non-reactive, non-metallic, almost as frictionless as PTFE, and can withstand temperatures to 2400 °F.
While the metal content of the anti-seize technology being used is important so, too, is the application method. Because brush-on application can be both messy and imprecise, new application methods have been developed, including a unique application device into which the fastener component is dipped, quickly and precisely coating the fastener with the ideal amount of anti-seize compound. This evenly applies the anti-seize compound around the entire component with any excess removed by a diaphragm fitted to the device when the fastener is withdrawn.
Anti-seize technology has come a long way since it was first developed decades ago. To learn more about the various anti-seize technologies and which one is right for your application, contact the anti-seize experts at Electronic Fasteners.